The term “flexible cold stamping†is not unfamiliar. The effect of cold stamping depends on the setting of various parameters in the operation. The coating amount of adhesive is also one of the key factors, so the choice of anilox roller is particularly important. Let us come today. Share how to control the amount of glue on the anilox roller during flexo hot stamping.
What is cold ironing?
Because of its particularity, cold-hot is also known as the "fifth color" in printing . Its essence is the combination of printing and laminating technology.
From the decorative point of view, the outstanding advantage of cold ironing is that it can achieve a variety of rich metallic colors by hot stamping, with silver anodized aluminum base, with the appropriate printing ink, can display most of the color, It is not necessary to store hot foils of various colors as hot.
Cold stamping can be full-page hot stamping or partial hot stamping, and can achieve a variety of decorative effects such as fine lines, halftones, dot transitions, hollowing, etc.

Label narrow-width rotary cold proof sample
Cold ironing system
According to different printing and feeding methods, the current mainstream processes include single-sheet offset printing and narrow-width rotary ironing. Single-sheet offset printing is mainly used in the packaging industry. The narrow-width rotary ironing is mainly used in the label industry. Flexo cold stamping is also the most commonly used cold stamping process for self-adhesive labels.
The flexo cold stamping system is mainly divided into four parts: coating UV adhesive, cold foil unwinding/foiling, adhesive UV curing and cold foil winding. The figure below shows the structure and working principle of a typical flexo cold foil system.
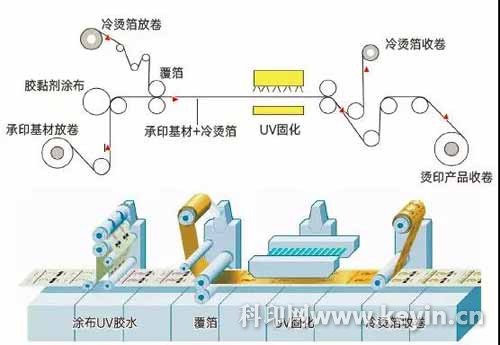
Schematic diagram of a typical flexographic cold-blowing unit
Flexo hot stamping effect depends on various parameter settings in cold-hot work, such as: adhesive coating amount, substrate selection, foil roll hardness and foil pressure, UV curing power, hot stamping speed, rewinding and unwinding Tension, peeling angle, etc.
Anilox roll
The amount of adhesive applied depends on the amount of sizing of the anilox roll. The correct anilox roll should be selected according to the hot stamping pattern and the substrate.
When hot stamping fine patterns, the amount of sizing of the anilox roller is smaller, and a high-number of anilox rolls are required. Conversely, if a large-area pattern is stamped, a low-number anilox roller can be used.
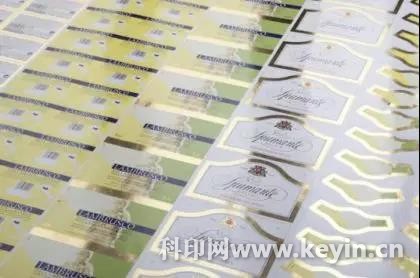
After printing, printing and glazing proofs
The printing substrate with smooth surface and weak absorption is less, and the amount of glue on the anilox roller is small; while the surface of the hot stamping surface is rough and absorbable, the amount of glue on the anilox roller is large.
The empirical data is: when hot stamping non-absorbent materials or plastics, the normal amount of sizing is 2 ~ 5g / m2, you need to choose the specification of 180L / cm, 6cm3 / m2 anilox roller.
Hot stamping materials such as paper can be considered from anilox rolls of 100L/cm and 14cm3/m2. However, it is not recommended to apply UV directly to rough and untreated substrates. For adhesives, it is recommended to apply the primer first.
The following table shows the parameters of the anilox roller corresponding to the high, medium and low grade standards of foreign cold stamping, for reference.
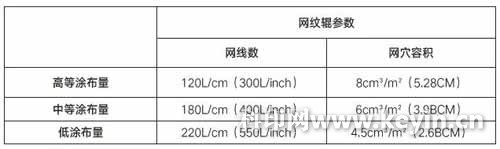
Anilox roller parameters corresponding to high, medium and low grade standards for domestic cold stamping
In the actual cold-hot operation, the amount of adhesive applied should be found in a practical standard configuration according to the specific requirements of the cold-hot stamping and other factors related to it.
Pure Water Wipes,Natural Cleaning Wipes,Pure Water Wet Wipes,Pure Water Wipes For Babies
Shandong Tianzige International Trade Co., Ltd , https://www.tianzigedipers.com